Chopper Frame Blueprints Pdf Viewer
Free detailed plans to build your own custom homebuilt bikes featured in Popular Mechanics, MAKE Magazine and Instructables.com. We'll show you step-by-step how to create unique bike choppers without spending a ton of cash.
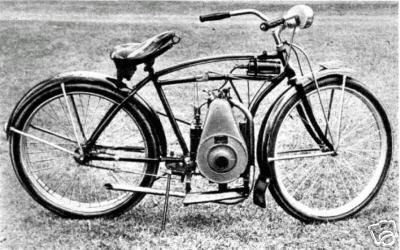

BUILDER: Jeff Palhegyi of Jeff Palhegyi Design Nothing worth doing is easy. This is true in life and in custom frame fabrication, a part of the motorcycle-building process that stems from a budding desire (if not necessity) to make a bike uniquely yours. What, after all, could be more rewarding than rolling down the road on something you welded together with your own two hands? Those hands won’t need to have been brazed by countless hours spent in a metal shop either. Sure, experience with a TIG welder and grinder will go a long way in making the job go more seamlessly, but trained hands are no more a mandate than a commitment to planning and willingness to learn something new.
Jeff Palhegyi of Jeff Palhegyi Design, a custom fabrication shop that works with to create special models such as the DT-07 flat-track bike, drives that point home, saying that, “The work leading up to fitting the first tubes is actually three times as difficult as actually assembling the pieces. You need to do the research and know exactly the parameters you want—the wheelbase, the head angle, seat height, engine dimensions, all of that.” There’s no industry standard, but generally speaking there are sets of numbers that work best for specific types of bikes, with Palhegyi adding that, “You’d be foolish to not look at what works and base what you’re doing around that.” Read books. Find articles on the web. Search everywhere and you will find the numbers you want.
Once you have the necessary information and know what pieces will go where, you’ll need to build a fixture, which will enable you to build your frame square and straight. Download Song U Smile Justin Bieber. While guys like Palhegyi use something that wouldn’t budge if you smacked it with a wrecking ball, know that yours will need to at least center on a flat table and components that are solid enough they won’t allow for movement in the welding process. Of course, “The stronger and more rigid the fixture is, the better the parts are going to be after the welding process,” Palhegyi explains. Movement is the enemy in frame building but also something that’s hard to avoid, as the heat generated from welding causes the metals (regardless of which kind) to shrink and pull. “You never know by how much,” Palhegyi suggests, but, “Whether it’s eighteen-thousandths or twenty-thousandths, you have to know that it’s going to move, and you have to plan for that.” Regarding materials, remember also that chrome-moly will be stronger and can be made thinner, so eventually it ends up being lighter, while steel is less resilient and heavier but also cheaper.
Don’t let the idea of shrinking metals intimidate you, as there are actually ways to limit the effects, one being to build subassemblies. These assemblies, welded together on a separate fixture, will pull and shrink as their individual pieces are fused together but in the end have a determined shape, meaning it won’t contort as you attach it to the other parts of the frame and throw things off even more. Also, you should tack weld pieces together and then weld the components up on either side evenly (similar to how you’d tighten all bolts evenly on an engine cover). “You weld a little here, a little there, and a little there, otherwise the frame is going to start to pull one way or another,” Palhegyi says. Sure, things can go askew. Or plans will change.